Automation in Mining: Where It Works, Where It Doesn’t, and What’s Next
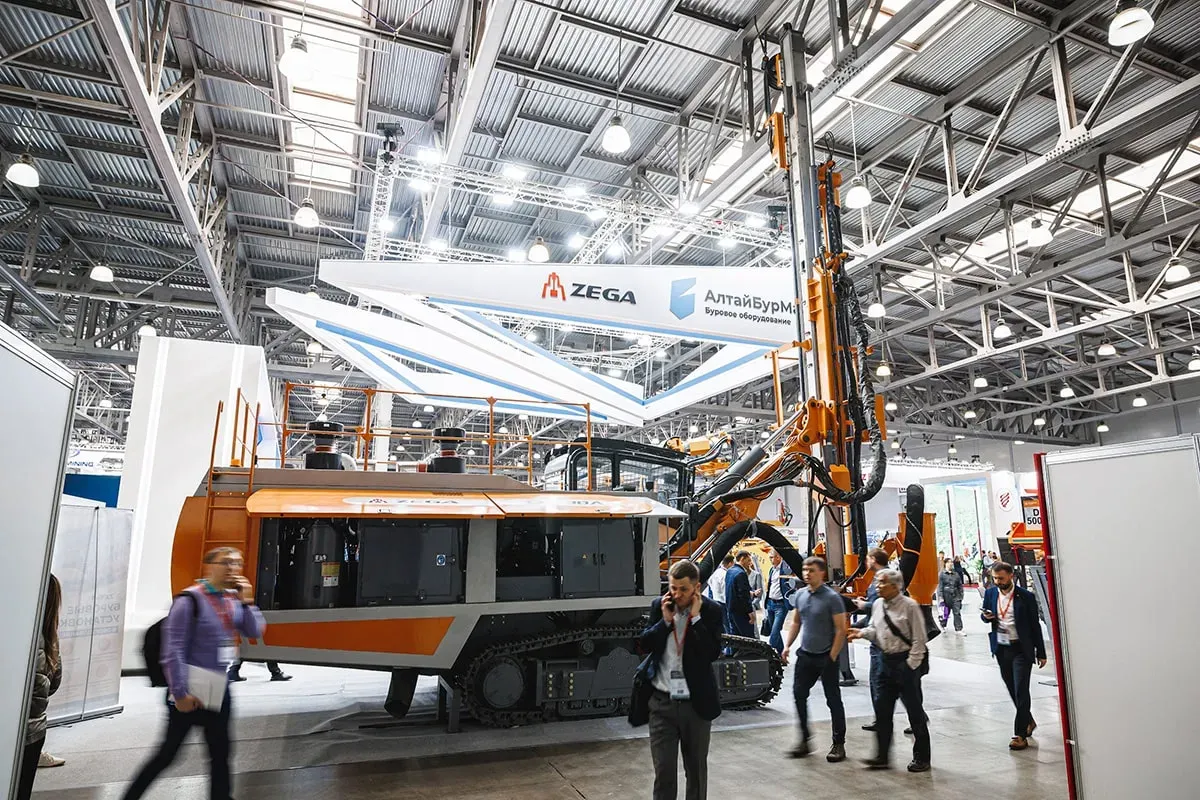
Automation in the mining industry continues to generate significant attention as companies explore new ways to improve efficiency, reduce risks, and maintain a competitive edge.
Will robots replace human jobs? At a highly automated mine in Sweden, the verdict appears to be “no.” Managers and union leaders at Boliden’s Garpenberg mine credit advanced technology for preventing closure and safeguarding employment opportunities. Their viewpoint highlights a crucial fact: when implemented responsibly, automation can create decent jobs, enhance on-site safety, and increase productivity.
This blog post examines how automation currently works in mining, where it encounters difficulties, and what lies ahead.
Where Automation Works in Mining
Automation has proven especially effective in haul truck operations. These vehicles can run continuously, 24 hours a day, without suffering from fatigue or shift changes. Fewer driver-related accidents occur because the trucks have consistent reaction times and precise control systems. Autonomous haul trucks operate continuously, reducing downtime and ensuring round-the-clock efficiency. Several leading companies have invested heavily in autonomous mining equipment due to its potential to reduce operational costs, protect workers from high-risk tasks, and increase overall site efficiency.
Furthermore, automated haul trucks have fewer variables to manage than other vehicles. They generally follow predictable routes, load and unload in clearly defined zones, and operate with advanced sensors that track terrain and proximity. This controlled environment makes automation more feasible and yields tangible safety gains.
Remote Monitoring and Process Plant Automation
Automated drilling and blasting systems also bring value to open-pit and underground operations. By allowing operators to control machinery from a safe distance, mines minimise the presence of personnel in hazardous locations. In addition, process plant automation, which has been common in chemical processing for decades, continues to advance in mining. Crushing, screening, and milling systems increasingly use real-time analytics to adjust process variables and improve resource recovery.
Moreover, advanced control rooms equipped with Internet of Things (IoT) sensors can oversee multiple sites simultaneously. This centralised approach refines decision-making by combining data from different production chain stages. The result? A more consistent workflow and streamlined operations.
Where Automation Falls Short
While automation can reduce the number of people on-site for specific tasks, it does not eliminate human presence. Many mines adopt partial automation, where workers and automated vehicles share operational zones. This mixture creates new challenges. Operators must ensure that drivers of manual cars understand how to interact safely with computerised trucks. Human-machine interfaces can become a hazard if workers lack adequate training, situational awareness, or clarity about system boundaries.
Integrating human-driven and autonomous fleets presents new safety challenges, requiring structured training programs and clear operational guidelines to prevent accidents. A minor oversight can lead to dangerous outcomes as vehicles move through the same haul roads.
High Costs and Infrastructure Requirements
Automation, especially at large scale, demands significant upfront investment. Mines need to upgrade digital infrastructure, install comprehensive sensor networks, and implement data processing systems. Small and mid-sized operations may find these costs prohibitive. The financial barrier can stifle technological adoption, particularly in regions where capital is scarce.
Furthermore, older mines might undergo extensive retrofitting to accommodate new machinery or control centres. This process includes upgrading connectivity systems, reorganising haul routes, and re-engineering pit designs to suit the predictable patterns of autonomous vehicles. Consequently, only some operations can pursue automation without significant disruption.
Skill Gaps and Workforce Resistance
Employers often face workforce resistance from employees who fear losing jobs to machines. However, the Boliden mine in Sweden shows a different reality: technology can help save and even create positions. Yet, resistance remains challenging if mine operators do not proactively train and upskill their teams.
Complexity in Underground Operations
Open-pit mines are early adopters because it is easier to navigate large, open spaces. Underground operations pose more challenges: limited network coverage, low visibility, and unpredictable geological conditions can hamper autonomous technology. Automation may only apply to specific tasks, such as remote drilling, rather than large-scale production in these cases.
What’s Next for Mining Automation?
As artificial intelligence (AI) matures, we can expect to see more sophisticated analytics guiding everyday mining decisions. AI-powered solutions rapidly process geological data, predict maintenance needs, and optimise production schedules. Robotics, built to withstand harsh underground conditions, will also become increasingly reliable, filling the gaps in complex extraction tasks.
Furthermore, new solutions will continue bridging the divide between equipment manufacturers and end users. For robotics and data management systems to be effective, OEMs (Original Equipment Manufacturers) must align their solutions with mining companies' operational needs. Likewise, mining companies must adapt internal processes to unlock the full potential of advanced automated systems.
The Importance of a System Safety Approach
Effective coordination becomes paramount when multiple types of automated equipment operate in the same zone. A system safety approach considers people, processes, and technology simultaneously. It analyses how human-driven vehicles interact with automated haul trucks, identifies potential points of failure, and proposes controls to manage these risks.
Additional sensor technology, improved communication protocols, and interoperable platforms can enhance the integration of different automated systems from various suppliers. Without a well-structured framework, sensor limitations or hardware incompatibilities can lead to accidents, especially if a computerised truck fails to detect a manually operated dozer or loader.
A Balanced Path Forward
Automation in the mining industry offers clear advantages but also presents challenges. While it enhances safety, productivity, and cost efficiency, successful implementation requires training, infrastructure, and safety protocol investment. By balancing automation with workforce development and structured integration, mining companies can maximise their benefits while addressing their limitations.
Strengthen Your Position in Automated Mining
Are you ready to explore cutting-edge solutions and witness the latest trends in mining automation? Attend our mining equipment suppliers expo to discover new technologies to reshape your operations. Learn more about autonomous mining equipment, connect with experts, and gain valuable insights into best practices.
Submit an exhibit enquiry to showcase your capabilities or join as a visitor to broaden your industry knowledge.
By taking these steps, you position your operation at the forefront of change, ensuring that your workforce and business can adapt to an increasingly automated future.